JQ Industries, a developer of flexible fiber sensors based in Weihai, has raised an eight-figure RMB sum in its Series A funding round. Backers include JHF, New Oriental, and Freyr Graphite. The company said the new capital will support R&D in robotic skin and haptic sensing, production expansion, and market development. InvesTarget served as the financial advisor.
This marks JQ’s second funding round since its founding in early 2024. A new round is already underway to secure funding for continued R&D, scale production, and build out the team.
JQ specializes in flexible fiber sensors made from plant-derived materials and textiles, aimed at use cases across robotics, healthcare, and automotives. Its portfolio includes both hardware like robotic skins and fingertip sensors, as well as software platforms for algorithmic processing, smart eldercare, and in-car comfort monitoring.
The rise of artificial intelligence and 5G communications has pushed demand for sensors that are adaptable, precise, and capable of functioning in complex environments. Flexible sensors are particularly relevant where conventional rigid sensors fall short, such as in motion tracking or pressure detection during physical interaction.
Still, most current flexible sensors are built on thin-film pressure technology, which is limited by issues with elasticity, breathability, and resistance to environmental interference. These constraints hinder performance and restrict mass production.
JQ’s answer is a fourth-generation resistive flexible fiber sensor. Its architecture deviates from planar films, using fiber-based layers for conductivity and sensitivity. The sensor integrates a fiber nylon core, a piezoresistive outer layer, and an electrode core—all within a flexible yarn.
This new material architecture offers exceptional flexibility and durability. The sensors can reportedly be folded to a radius of less than 0.1 millimeters and have passed automotive-grade impact tests. They retain high elasticity and rebound performance without requiring recalibration and demonstrate strong resistance to environmental interference. When integrated into textiles, the sensors remain breathable and comfortable against the skin, making them suitable for diverse use cases.
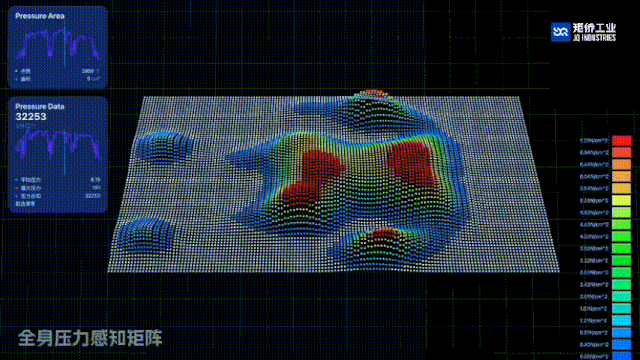
“We’re now heavily focused on humanoid robotics and scaling fiber sensors into large-area electronic skin,” founder Zhang Jingqi told 36Kr. “These robotic skins can help robots sense their environment more holistically, interact like humans, and ensure safer human-robot interaction. For example, foot-embedded sensors can detect surface hardness and balance to help robots walk more stably.”
According to Zhang, the company’s woven fiber sensors offer distinct advantages for humanoid robotics. He cited the G1 skin suite from Unitree Robotics, which includes glove, torso, and sole components, as a representative application. The suite provides high levels of flexibility, elasticity, breathability, and durability. The gloves deliver multi-point tactile feedback across the palm and support both motion capture and remote manipulation. They accommodate joint folds down to zero and can detect forces as low as 0.01 newtons, with a pressure sensitivity range up to 3,500 kilopascals. When integrated with Nvidia’s Isaac Sim, the sensors enable tactile data modeling and deployment in closed-loop systems.
The company is currently negotiating with over ten humanoid robotics companies to supply upper-body and limb skin systems. Some units are already being shipped in volume.
Beyond robotics, JQ is extending its sensor technology to eldercare and smart mobility. It has signed partnerships with institutions like Tian’e Daojia, Taikang, and Yuecheng Senior Living. Its eldercare mattress monitors pressure distribution, posture, sleep quality, and breathing to detect early signs of bedsores or falls.
In the automotive sector, JQ is working with major carmakers to embed its sensors into cockpits. Use cases include comfort tuning and gamified car seat experiences. Some of these integrations are now entering mass production.
One of the biggest hurdles in sensor commercialization is manufacturing consistency. JQ has addressed this by building its own factory, retrofitting textile machinery, and optimizing dyeing and finishing. These changes have cut production costs by 80% and improved yield consistency by 200%.
The firm now runs an industrial roll-to-roll line capable of producing 200,000 sensors annually at a 95% yield. New samples can be prototyped within 24 hours.
JQ’s team of 30 includes alumni from the Chinese Academy of Sciences and top hardware firms. Zhang, who holds a degree in electronic engineering from the University of York, previously served as CTO at a Xiaomi ecosystem company.
“JQ Industries delivers a compelling solution in embodied haptics. True full-body robotic skins require scalable, cost-effective, and reliable solutions,” said Zhou Lifeng, a partner at JHF. “JQ’s fiber-textile approach enables a rare combination of flexibility, sensitivity, accuracy, range, durability, and affordability.”
KrASIA Connection features translated and adapted content that was originally published by 36Kr. This article was written by Zhang Zhuoqian for 36Kr.