After a lengthy chapter, Nio has seemingly secured qualifications from the government to operate as an independent vehicle manufacturer. Recently, the automotive manufacturer appeared in the “Vehicle Manufacturing Enterprise Credit Information Management System” of China’s Ministry of Industry and Information Technology. This development essentially suggests that Nio can now produce vehicles under its own name rather than outsource the process to a partner. In the case of Nio, that partner has primarily been Anhui Jianghuai Automobile Group (JAC Motors).
In China’s tightly regulated automotive industry, production necessitates specific qualifications. Typically, approval is required from the National Development and Reform Commission (NDRC) for investment and the Ministry of Industry and Information Technology for the production base and product quality. While these qualifications help manage overcapacity, they pose a significant challenge for emerging car manufacturers.
Under current policies, newly established car companies may find it challenging to obtain investment permits for new projects due to stringent application requirements. Securing these qualifications may have been a prolonged process for Nio, but their impact will extend beyond the application and evaluation stage, influencing the company’s growth plans in the near future.
In October this year, JAC announced the sales of its relevant factory assets, which it later disclosed would be acquired by Nio and Hefei State-owned Assets Holding separately for RMB 31.58 billion (USD 4.42 billion) and RMB 14.18 billion (USD 1.98 billion) respectively. While Nio’s primary focus has been to increase sales and boost its revenue by streamlining its team to sustain operations, this transition will undoubtedly add responsibilities to Nio and could create distractions. This may also explain the subdued response from the capital market to Nio securing the qualifications.
In the long run, however, being able to operate as an independent manufacturer may enable Nio to compete more efficiently.
Missed opportunities for Nio?
In China, car production is an industry with strict entry requirements. Several years ago, however, a loophole was opened to encourage new players in developing new energy vehicles. The NDRC issued new regulations in 2015 allowing relevant companies to obtain production qualifications for pure electric vehicles. From March 2016 onwards, this move saw 15 companies receive qualifications to produce EVs in a little over a year.
This was the first opportunity for new entrants like Nio (at that time) to acquire qualifications. Yet, due to factors such as the timing of entry and progress with product development, a significant number of these players missed the window of opportunity.
An insider told 36Kr that Nio had intended to apply for the qualifications with the ES8, its first mass produced car. However, by the time appropriate arrangements had been made, the application window had already closed.
The NDRC might have underestimated the appeal its regulatory change had created, opening the floodgates for pure EV projects as dozens, if not hundreds, of new car companies emerged. The issuance of new EV licenses was urgently halted in the wake of this development.
Jianghuai Volkswagen were among the last batch of licensees announced in June 2017. Subsequently, new entrants could only produce cars using two methods: acquire the necessary qualifications from existing car companies or collaborate with them through outsourcing.
Companies like Xpeng Motors, in a similar plight to Nio, veered toward the former. For example, at the end of 2018, Li Auto acquired Chongqing Lifan Automobile (Lifan Group) for RMB 650 million (USD 90.9 million). Others like Xpeng and Leapmotor pursued both options simultaneously, seeking partners for outsourcing while attempting to acquire qualifications.
Nio was an exception, choosing only the outsourcing route. A year after the ES8 was launched, it began mass production in a new factory built by JAC.
At that time, William Li, chairman of Nio, thought that outsourcing was a more stable option and would alleviate the company’s operational load. He emphasized using the company’s existing resources to create new vehicle models and develop user communities.
An individual who had interacted with Li before told 36Kr that while several people had advised Li to acquire qualifications at that time, he did not buy into the idea, questioning the point of spending billions of RMB for that reason when it was possible to produce cars regardless (through outsourcing arrangements).
Li’s judgment was not baseless. After the suspension of production qualifications for new energy vehicles, the NDRC formulated new investment regulations at the end of 2018. Although the revised policies still provided space for new entrants, approval authority for new projects was delegated to provincial governments, as long as companies and regions met specific conditions.
These conditions were mainly established to control capacity, such as requiring companies to achieve cumulative sales of 30,000 vehicles or cumulative sales exceeding RMB 3 billion in the last two years. Additionally, within a province, the capacity utilization rate for the last two years must exceed the average level, and all newly built pure EV factories must be in full production to secure approval.
An insider told 36Kr that meeting these conditions wasn’t easy. Despite decentralizing approval authority to local governments, guidance from the NDRC was nonetheless required, making it “very difficult” to secure approval.
This process has troubled numerous new car companies in the past few years. Xiaomi, which recently entered the scene, initially faced this challenge. One reason for the abrupt halt of Li Yinan’s car project last year was that Dorcen, its partner, did not secure approval.
Outsourcing isn’t a long-term solution
Initially, the outsourcing model seemed appealing. In Nio’s collaboration with JAC Motors, the latter invested in building the factory while the former was responsible for purchasing the production equipment. All Nio needed was to deploy a team to collaborate with JAC— it did not need to build its own factory, and the overall asset-based operations were relatively light. This team also did not need to start from scratch as it absorbed JAC’s capabilities.
Inherent risks of outsourcing that typically face criticism, such as quality control issues and limitations on capacity expansion, were largely mitigated by Nio by customizing the nature of its collaboration with JAC.
Chairman Li once explained that Nio’s collaboration with JAC was not purely an outsourcing arrangement but rather a manufacturing partnership. Nio was actively involved in the production process spanning technology utilization, management procedures, and quality control measures.
Moreover, outsourcing arrangements are generally fulfilled by refurbishing the existing facility of manufacturers. Nio’s partnership with JAC was different as it involved constructing a new factory from scratch, designed entirely based on Nio’s technological requirements. Consequently, Li confidently stated in an interview that this factory may even surpass Porsche’s.
However, this partnership model was not easy to execute. The teams from Nio and JAC had to undergo a long period of adaptation, with an insider privy to the matter telling 36Kr that JAC’s team held significant influence over the process in the first few years of the partnership. As the model was novel and it was the first time Nio and JAC were collaborating in this fashion, resource allocation and various aspects were left in a vague state, leading to disputes.
Financing was another significant aspect. Although Nio was thought to pay JAC based on the production and processing costs per vehicle unit, the actual costs were higher in reality to account for other expenses.
For instance, based on Nio’s annual report, in addition to the per-vehicle production and processing fees, Nio also paid JAC for depreciation and amortization of relevant assets, purchase of production materials, and related taxes. Compensation for the investment in the F1 factory was also required. In 2020, 2021, and 2022, Nio paid JAC fees of RMB 530 million (USD 74.7 million), RMB 720 million (USD 103 million), and RMB 1.13 billion respectively (USD 159.4 million).
To clarify such disputes, Nio and JAC jointly established Jianglai Advanced Manufacturing Technology in May 2021 to oversee operations. The procurement authority for production materials also shifted from JAC to Jianglai. This change improved overall operations though the effects were only notable starting the second half of 2022.
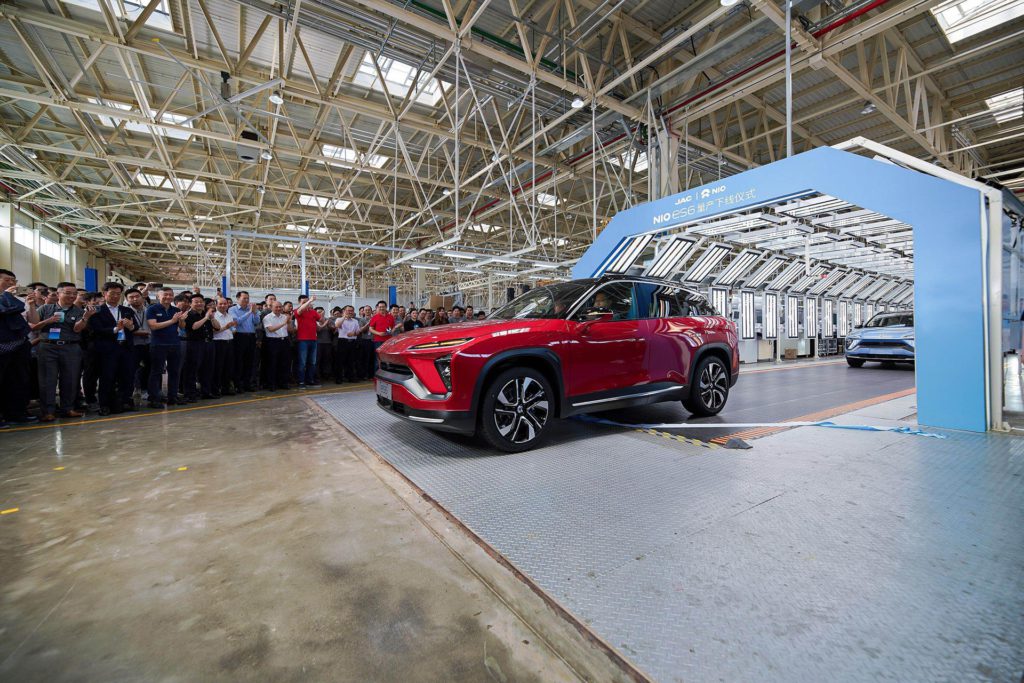
However, for most car companies, outsourcing ultimately remains a somewhat restricted approach. Even though such arrangements allow flexibility to assume authority over the production process, there are business dynamics and management complexities that still require accounting for which might pose potential risks to the efficiency of the production process.
At the end of last year, Nio announced the transfer of certain production facilities in the factory to JAC. 36Kr was told that this was done to comply with ownership requirements for fixed assets under the outsourcing model. The related facilities needed to be transferred to JAC’s name, and Nio paid a significant amount in taxes to complete this transfer. However, as of the release of the annual report in 2022, JAC had not yet paid the related consideration.
This year, with Nio making a breakthrough by securing its own qualifications, its collaboration with JAC has also begun to change.
In October this year, JAC announced that it would transfer certain assets, including its inventory, fixed assets, and ongoing projects related to its third factory for passenger cars, as well as buildings, structures, and equipment of its Xinqiao factory. These assets were confirmed to be the factories where Nio produced its cars.
The assets JAC put up for sale were substantial, with an assessed value close to RMB 4.5 billion (USD 634.8 million). Nio would purchase inventory, fixed assets, and ongoing projects of the third factory and buildings, structures, and equipment of the Xin Qiao factory, spending over RMB 3.158 billion (USD 445.5 million). This is not a small amount of money for present-day Nio.
Car production is an efficiency-based competition. Industry leaders like Tesla and BYD focus on squeezing efficiency at every stage of manufacturing. Factories are designed and operated as meticulously crafted products. Tesla’s Shanghai factory, averaging 45 seconds to produce a car and achieving a production output per unit area several times higher than its peers, is the epitome of optimal production efficiency. This efficiency has allowed Tesla to maintain a high gross profit level and confidently adjust prices amidst fierce competition.
In the long term, obtaining independent qualifications is the beginning for Nio to enter the mainstream path of car manufacturing. Fully controlling all core aspects of automotive production will enable Nio to gradually improve manufacturing efficiency and secure more advantages in the intense market competition.
KrASIA Connection features translated and adapted content that was originally published by 36Kr. This article was written by Peng Suping for 36Kr.