Since 2016, Pune-based molecular diagnostics company Mylab Discovery Solutions, a firm started by Hasmukh Rawal and Shailendra Kawade, has been manufacturing test kits for several diseases locally. For several years, the company went by without attracting much attention—there wasn’t any reason for it to be at the center of public interest.
This spring, that changed. On March 23, Mylab became the first company in India to manufacture testing kits for the novel coronavirus, which has claimed thousands of lives in the country and paralyzed the economies and healthcare systems around the world.
Mylab had not anticipated that India would be hit hard by the coronavirus. But in early February, when people who had returned from Wuhan to the South Indian state of Kerala tested positive for COVID-19, the company decided to redirect its resources and be prepared.
“We didn’t think SARS-CoV-2 would come to India and we wishfully thought it would be contained before it could reach here,” Hasmukh Rawal, co-founder and managing director of Mylab Discovery Solutions, told KrASIA. By mid-February, the company made preparations to develop its capabilities to manufacture what is now the most sought-after testing kit in the world. “We never imagined India would need so many testing kits,” Rawal said.
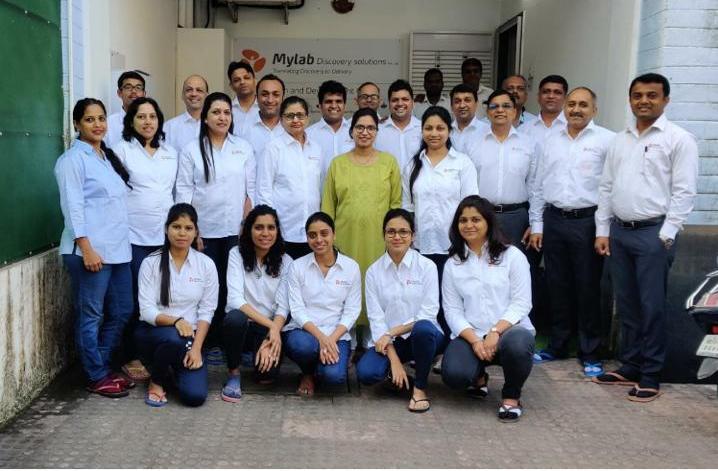
Right now, India, like many countries, is on a global hunt to procure testing kits for COVID-19. And finding the right sources can be difficult. For instance, over 500,000 test kits bought from two Chinese companies, Guangzhou Wondfo Biotech and Zhuhai Livzon Diagnostics, have been found “under-performing” by the Indian Council of Medical Research. Establishing a stable domestic supply is a significant step for any country’s efforts to containing the pandemic.
In March, when Mylab was given a go-ahead from the relevant health authorities, its production capacity was still far from what was needed in India. By the end of the month, India was testing only 1,900 people per million. There was still a dependency on imported kits made by Swiss firm Roche. The Indian government placed orders for at least a million more kits from the World Health Organization (WHO).
At first, Rawal said, Mylab had the daily production capacity to make around 100 test kits, which altogether could process 10,000 samples. A ramp-up would give the company the means to manufacture enough kits to test 200,000 to 300,000 samples a day.
Staying local
Rawal, who is also a bio-technologist by profession, said it took the Mylab’s team of 50 people six to seven weeks to develop COVID-19 test kits that match the standards set by the WHO and US Centers for Disease Control.
The company claimed its kit, called PathoDetect COVID-19, reduced processing time for tests from 7.5 hours to 2.5 hours. The company uses the reverse transcription polymerase chain reaction (RT-PCR) detection method to actively identify the coronavirus’ presence, rather than the antibody rapid testing technique, which looks for antibodies that are present after infection.
With the local production of test kits in gear, Rawal said testing costs have reduced significantly—from INR 4,500 to INR 1,200 (USD 16).
“Our belief is that a country should be self-sufficient to locally produce at least the life-saving tests so that everyone can afford it. When you import test kits, it automatically becomes expensive, plus multinational companies have their own overhead,” Rawal said.
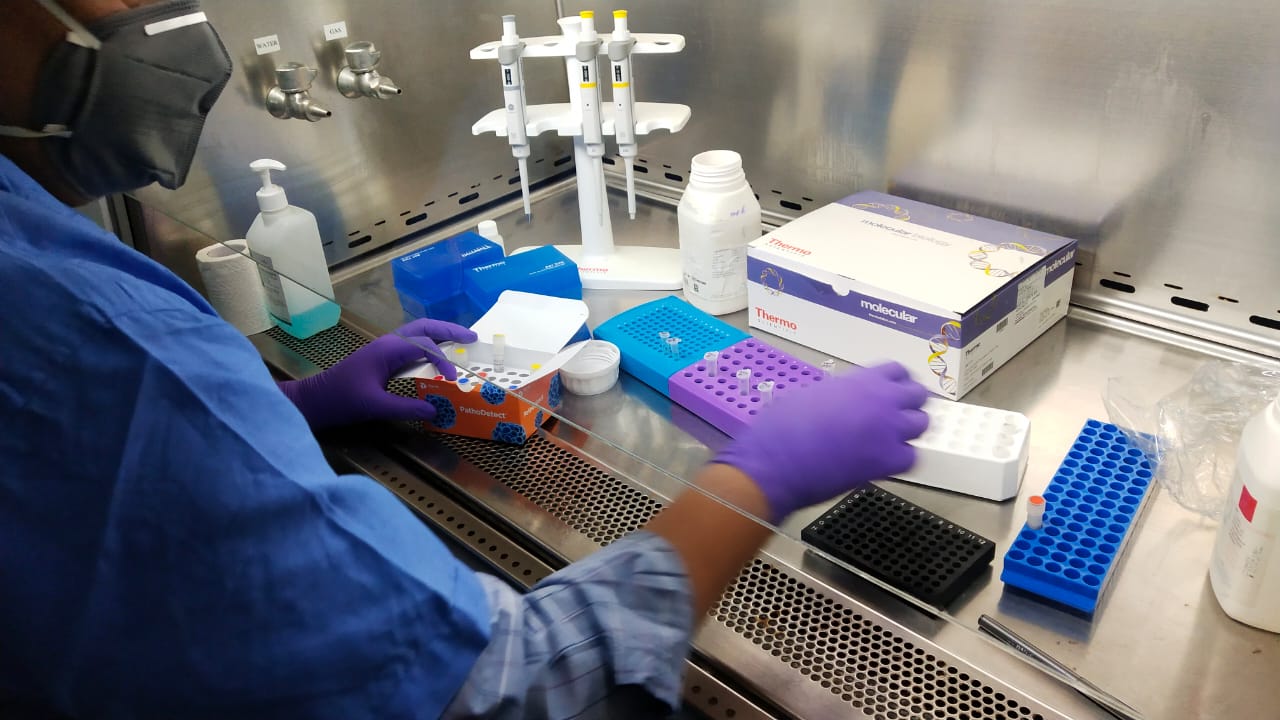
Mylab has detection kits for various viral, bacterial, and parasitic diseases, such as chikungunya, cancer, and tuberculosis. The firm was the first company in India, and third globally, to manufacture individual donor nucleic acid testing (ID-NAT) kits to detect and quantify HIV-1, hepatitis B and C, and human papillomavirus (HPV).
These testing capabilities are particularly important for India as it fills blood banks for medical emergencies. “Before the blood is given to the patient, it must be tested for several viruses. . . but since the test is very expensive in India, we have not made it mandatory. By making these test kits in India, we are able to reduce the cost by one-third on every product,” he said.
Going global
Mylab has been seeking funding for two years, but didn’t land any investors until recently. Within a fortnight after developing commercially viable COVID-19 testing kits, the company received a multi-million-dollar investment from the Serum Institute of India and AP Globale.
With the involvement of Serum Institute of India, which has a global presence, Mylab will be able to ship its testing kits to overseas markets in the coming years.
In addition to this, the diagnostic kit manufacturer also received a grant of INR 10 million (USD 131,500) from the Action COVID-19 Team, a USD 13 million fund set up by top technology investors and entrepreneurs.
The company will use the cash to bolster its coronavirus test kit production capabilities, as well as launch new products in the coming years. “Right now, we are focusing on expansion and production capacity. Plus, we have some huge projects in mind, so a large chunk of the money will be spent on research and development. The new product should be ready by 2025,” Rawal said.
In January, Mylab showcased a box-like machine called Compact-X that the company claims can simultaneously test 96 different samples without human intervention, generating results for tests covering cancer, bacterial or viral infections, and blood work. The machine is showcased by Mylab as capable of analyzing blood, plasma, tissue, sputum, and swabs from humans as well as animals. Rawal called it a laboratory in a box.
Even though, in the past, Mylab has developed products that are more complex than COVID-19 test kits, such as ID-NAT, Rawal said that “sometimes being prepared to tackle a global issue with a product which might not be that superior but much needed, is all that takes to take you to the higher limb of glory.”
This article is part of KrASIA’s “Startup Stories” series, where the writers of KrASIA speak with founders of tech companies in South and Southeast Asia.