On a regular day, 3D printing firms such as Siege Advanced Manufacturing and Additive3D Asia do both mass and customized 3D-prints.
When COVID-19 hit Singapore however, their businesses were disrupted and they witnessed their revenue falling by at least 70%, as clients cut back on their marketing dollars and cancelled events.
Amid a global shortage of personal protection equipment (PPE), a number of them converted the majority of their 3D-printing capacity and joined the ranks in producing PPE such as face shields, nose swabs, and surgical mask straps.
We spoke to a few 3D-printing companies in Singapore to find out how they have had to adapt and adjust their business in order to rise to the challenge of the pandemic.
Converting 90% of the printing capacity
For Daphne Ting and Loh Chi Jie, co-founders of Siege Advanced Manufacturing, their regular 3D-printing business was badly affected when the outbreak started to worsen in February and as supply became an issue with nation lockdowns.
They reportedly have the largest 3D-printing capacity in Singapore, with 50 3D-printers at their Ang Mo Kio Industrial Park facility.
She added that countries and hospitals worldwide were facing shortages of PPE to protect themselves while treating COVID-19 patients. Basic items such as surgical masks and protection gowns were scarce and it was an alarming sight.
“We read in the news about how medical workers in Malaysian hospitals were using trash bags and cling wrap as PPE due to shortages,” she said.
They decided to take it upon themselves to do something about it since they had the printing capacity to help. They then reactivated their manufacturing lines to produce face shields.
Several innovative designs for 3D-printed face shields were going around and they quickly started producing their first face shield using one of the designs from overseas—the Czech Republic’s Prusa reusable face shield.
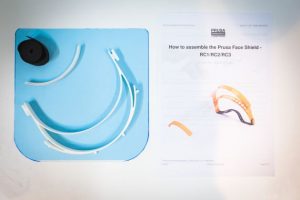
A typical face shield consists of four separate parts: Two 3D-printed parts, one transparent sheet, and one elastic band.
They 3D-printed the parts at their production facility, and sourced externally for the transparent sheet and band. Once all the parts are all in, they manually assembled the face shield.
Another 3D-printing company that specializes in industrial 3D-printing called Additive3D Asia, started off when they were asked to help a charity organisation in Mozambique, Africa which urgently needed face shields for medical frontliners.
Today, more than 50% of their production capacity has been converted to printing PPE.
Read this: This Singapore startup marries 3D-printing with orthodontics for big smiles
After Daphne and Chi Jie listed their initiative online, they received an influx of donation requests from health entities across Asia, and the number of face shields required are in the thousands.
As much as they wanted to donate the face shields, the raw materials that go into each face shield such as the plastic sheets, elastic bands and utilities cost money — which means that they would not be able to sustain donations for long.
This sparked their crowdfunding campaign. Their initial initial crowdfunding goal of SGD 13,000, which would have enabled them to produce 2,000 shields, was met with great support.
On April 11, they raised the goal to SGD 16,000, pledging 2,500 face shields in total. To date, they have raised over SGD 19,000, which is equivalent to about 3,000 face shields.
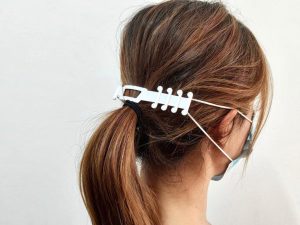
The duo has donated thousands of face shields to Singapore organisations, hospitals, as well as countries such as Indonesia, Malaysia, and the Philippines.
When they were giving out the face shields in Singapore, they heard quite a number of complaints from people (hawkers, Grab drivers etc) regarding the pain they experienced behind their ears due to prolonged wearing of the face masks.
To solve their pain point (literally), they started printing a plastic tension release band to hold the elastic straps of surgical masks at the back of the head, which helps provide relief from discomfort around the ears.
Called “ear savers”, the bands significantly alleviated the discomfort face mask wearers faced.
Since these ear savers are quite fast to manufacture and not very expensive, they decided to give them away on their website and online marketplace Carousell.
As of writing, they have produced 7,050 face shields and 25,620 “ear savers”.
Daphne shared that they are also currently producing 3D-printed nose swabs practice kits—for swab testers to practise with—and counter shields for customer-facing workplaces as we prepare to enter Phase 2 of the circuit breaker.
Now, they are producing up to 250 face shields a day, or 2,000 “ear savers” a day.
Besides donating what they manufacture, they also sell the face shields and “ear savers” but Daphne revealed that they don’t actually earn a lot from it.
Businesses and individuals join forces
Another 3D-printing company that has also jumped onto the bandwagon to manufacture PPE is Creatz3D Pte Ltd.
Before the outbreak, Creatz3D specialized in professional industrial-grade plastic, metal, and ceramic 3D-printing solutions.
They have since shifted their focus to producing nasal test swabs, hands-free door openers, face shields and even medical manikins.
Interestingly, for the medical manikins, Sean Looi of Creatz3D said that it was a request that came up as Singapore was looking to increase swab tests and train front-liners.
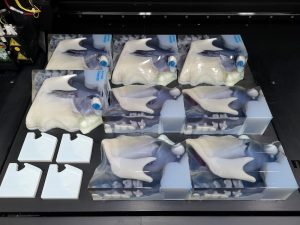
Just like Siege Advanced Manufacturing, Creatz3D is a member of the National Additive Manufacturing – Innovation Cluster (NAMIC).
As the national AM (Additive Manufacturing) accelerator, NAMIC is responsible for orchestrating and implementing breakthrough strategies for the future of additive manufacturing—also known as 3D-printing.
After the initiative came about, individuals came forward to help print PPE in their personal capacity, which could be just a single printer they have at home.
“Designs were of open-source and can be obtained online,” said Colin of 3D-Print Singapore, another printing services provider that switched to PPE manufacturing.
In other words, anyone with a 3D-printer can theoretically do the manufacturing. Soon, the 3D-printing community was printing “ear savers” from their homes.
“If you have a 3D-printer, it is very easy to manufacture the “ear savers”, all you need is a 3D design file and a 3D-printer,” said Daphne of Siege Advanced Manufacturing.
3D-printing has its own challenges
“However, for the face shields, it is not as simple and takes quite a bit more work and resources. The nose swabs and counter shields are also not as simple,” she added.
As most face shields and “ear savers” were manufactured for individuals, they do not require regulations, said Colin of 3D-Print Singapore.
“However, if you are donating to a medical facility, the regulations will definitely be a lot stricter,” said Daphne of Siege Advanced Manufacturing.
“For example, nasal swabs will require more stringent regulatory requirements compared to, say, the manikins,” added Sean of Creatz3D.
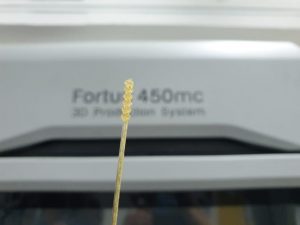
For the medical manikins, the requestor did not provide them with any files to get started on the project which was due over a weekend. They had to rely on their expertise and experience to deliver the project.
While individuals were able to use their own 3D-printers, Sean was quick to highlight that 3D-printing was never a fast-production technology.
“Unless you have multiple systems, it’s difficult to start production with one machine,” he said.
Echoing Sean, Paulene Siew, managing director of Additive3D Asia, said that “3D-printing is ideal for low volume quantity and customizable products.”
The challenge then lies in the fact that 3D-printing is not suitable for mass manufacturing of huge quantities.
Sharing more about the challenges, Daphne said that securing the supply of materials at the start of their donation campaign was a huge headache.
“Even if you have the idea to manufacture face shields, obtaining materials in a time of lockdown is just so difficult.”
“The uncertainty of shipments, whether your materials will arrive in time or whether you can get the face shields to other countries, is also a challenge,” she added.
To avoid delays as much as possible, her colleague has been sleeping in the office for two months to manufacture the face shields and “ear savers”. They were fortunately exempted from suspension during circuit breaker so they could continue printing these essential PPE.
Another challenge they faced was getting the PPE to people who need them.
“For the “ear saver” giveaway, we conducted it through Carousell and due to the circuit breaker, we were not able to allow self collection. Hence, additional work had to be done to mail out every single “ear saver”, said Daphne.
The future of 3D-printing beyond COVID-19
3D-printing has helped us see for ourselves the possibilities of the technology.
Thanks to it, critical life-saving ventilators and respirators were 3D-printed and supplied faster in other countries.
“Many companies are revisiting how products are being manufactured and some are thinking of ways to bring manufacturing back locally,” said Terry Ming, division manager of Engineering Computer Services Singapore.
As a quick interim solution till mass manufacturing processes come into the picture, 3D-printing allows people to test out ideas before designs go mainstream, he added.
On the other hand, Daphne shared that they are looking to further expand on their e-commerce and online services to reduce the need for face-to-face interaction, such as online quotations and consultations, and even a virtual 3D-exhibition.
This article was first published by Vulcan Post.